Assembly station based on a magnetic levitation system

E-Mail: | binnemann@match.uni-hannover.de |
Team: | Lars Binnemann |
Year: | 2021 |
Funding: | DFG (PhoenixD) |
Duration: | 4 Jahre |
While product development cycles decrease, product variety increases. In addition, production costs must be reduced to remain competitive. This results in major challenges, especially for production technologies. In order to meet the continuously changing requirements, the manufacturing systems used must have a high degree of flexibility. To develop such a system magnetically levitation system offer a great opportunity. These systems consist of a stationary stator made of electromagnets and a workpiece carrier (mover) made of permanent magnets. By controlling the electric fields, the mover hovers above the stator and can be positioned in six degrees of freedom. The arrangement of the stators is flexible (e.g. as a plane or as a ring). Here, it is possible to control multiple mover independently on the same stator-cluster. Traditional these planar motor system are used for the workpiece transport between the single process steps. To reduce the production investment costs the mover should not only be usedfor workpiece transport but also for funktional movements during the process steps. The goal is to represent the hole production process of optical systems. These include, for example, assembly, sputtering and measuring processes. A modular design allows the stations to be connected in a flexible order. This makes it possible to adapt the machine to constantly changing requirements. For such an inline production machine the match is developing and investigating a corresponding assembly station. Here, all movements for positioning and aligning the workpieces are performed by the mover. Only one additional vertical axis executes the assembly or place movements. Among other things, the system behavior during assembly processes will be investigated. In addition it will be investigated how a high (assembly) precision can be achieved even with significantly lower stiffness compared to traditional axis systems. Furthermore, new sensor guidance concepts will be developed to reduce the investment costs. The aim is to capture all relevant ( geometry) data using just one camera and one distance sensor.
Contact: Lars Binnemann


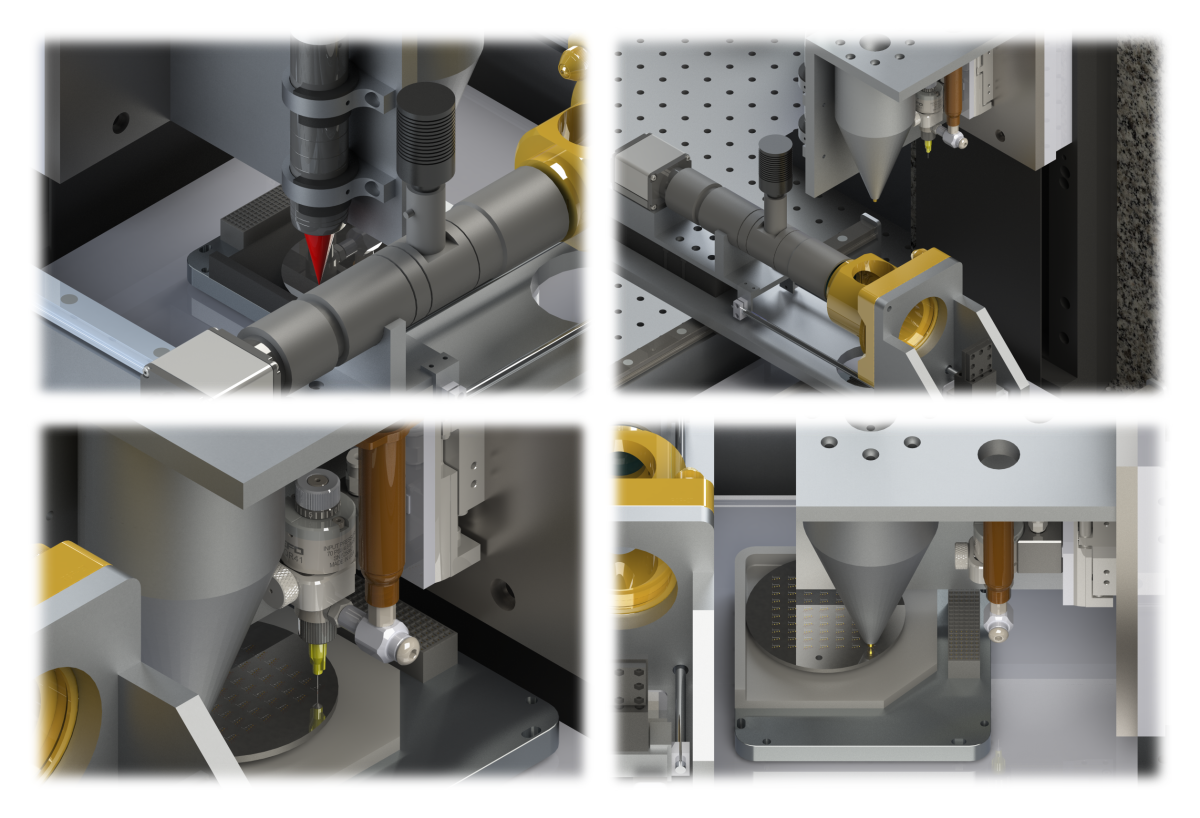
Process sequence at the assembly station. Top left: Measuring & leveling; Top right: Measuring and aligning; Bottom left: Adhesive application; Bottom right: Assembly